When an automotive parts supplier needed a unique robotics application that required customization of a MiR top module, local distributor Allied Automation connected them with the trusted team at Hyperion Automation.
Previously, the automotive supplier used carts and physical labor to pick parts for an assembly kit or to move parts around the floor, sometimes with a forklift. Through Hyperion’s solution, the automotive supplier reduced labor costs, better utilized employee time, increased floor efficiency and improved employee safety. Instead of an employee walking around with carts to pick up various parts, Hyperion created a top module for a MiR (Mobile Industrial Robot) with a zoned side-loading top module that would travel a predetermined pathway to pick up parts from multiple conveyor lines.
The Challenge
The Hyperion team faced multiple customizations challenges.
- Creating a kit required multiple products of unique heights and weights which were then loaded from an existing conveyor 30 inches off the floor, far taller than a standard top module.
- The MiR needed to be able to load all 4 of these parts individually from different areas on the floor and then unload the entire kit at the end of the line.
- For the ease of use, the system needed to use Mitsubishi PLC controls that employees were already familiar with.
The Solution
Finding the Right Top Module
To complete this task successfully, the Hyperion team customized a side-loading top module for a MiR500. The larger of MiR’s models, the 500 better supported the size and height of the top module, preventing possible balance issues.
The height of the top module allowed easy integration with the 30 inch existing conveyor while the side-loading feature maximized floor space. Using a side-loading top module requires less maneuvering space because it can simply pull alongside a station to load and unload parts instead of having to back up and swing around. For more detail on the differences between front- and side-loading top modules, read our blog on AMR customization.
Rolling, Rolling, Rolling
To successfully load a full kit, Hyperion fitted the top module with two conveyors, each split into two zones with their own motors or driving rollers. This structure created a total of four quadrants to accommodate four different parts. Using these conveyors, the robot would pick up Part A, weighing 90lbs from the first station and use a system of sensors and the individually zoned conveyors to move that part to the back.
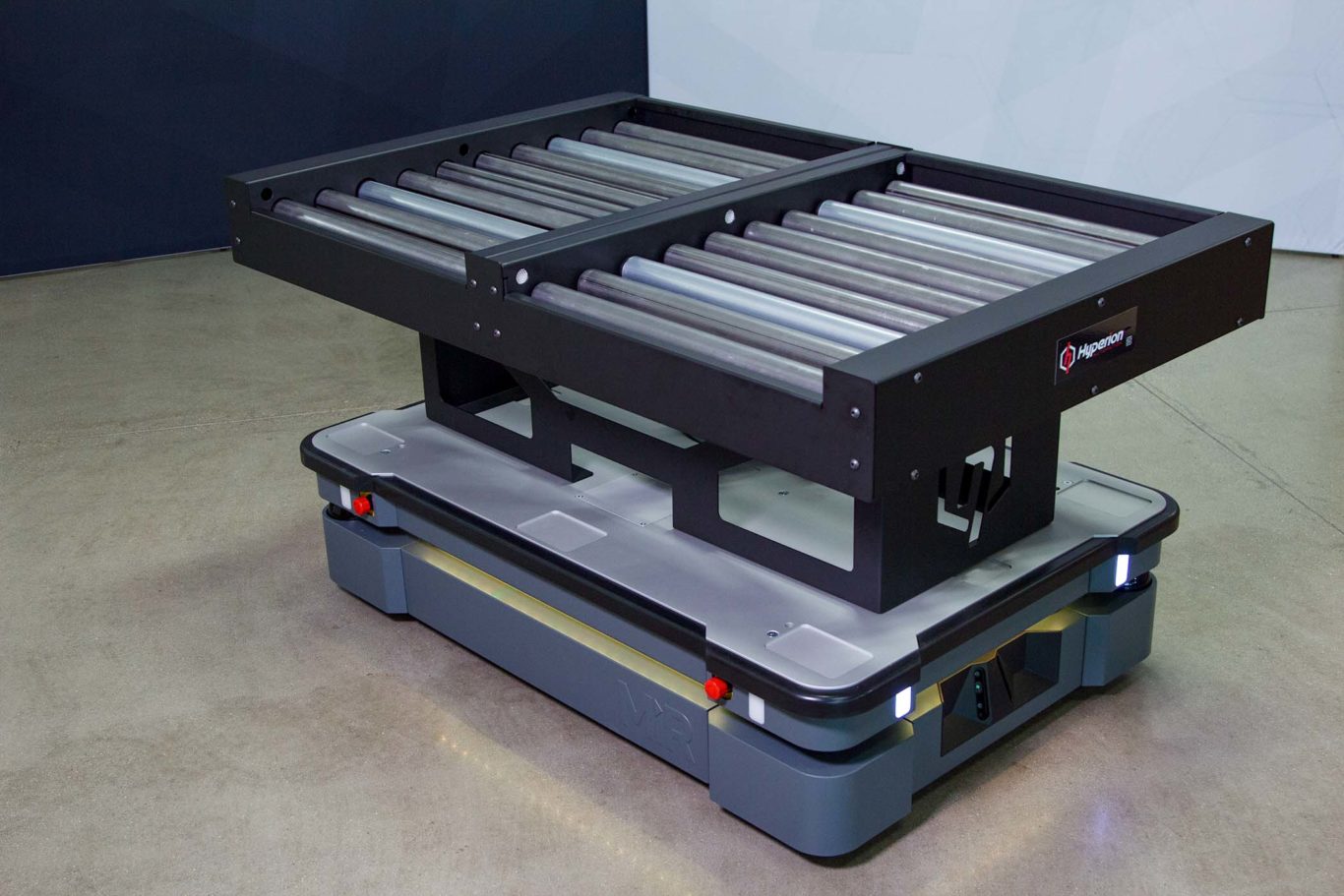
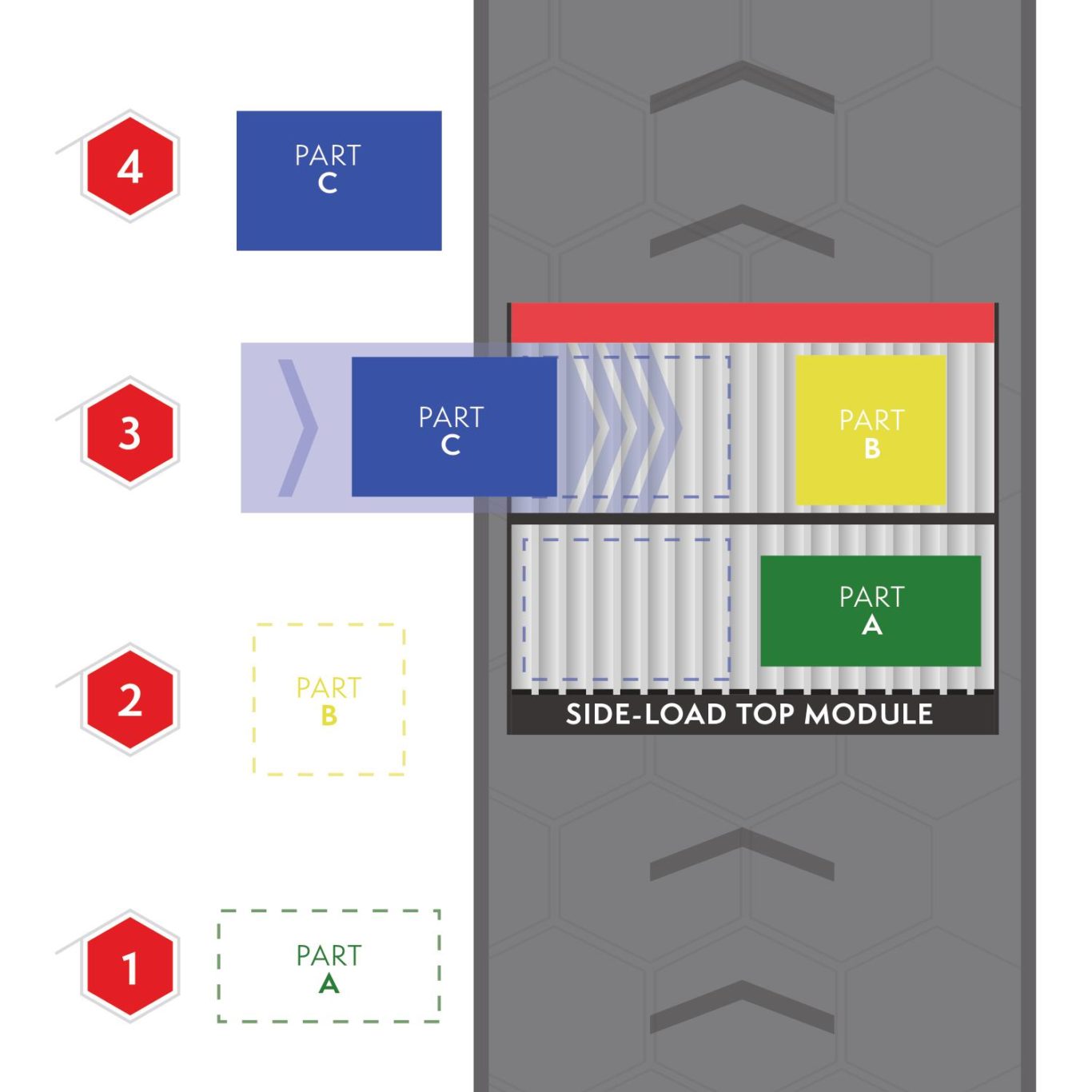
Product Presence Sensors
Both conveyors used three sensors in order to position and load parts in their proper place.
- One sensor mounted to the back told each motor/driving roller when to stop as a part reached the back.
- Another sensor in the middle detected when the second set of parts reached its proper place.
- A third sensor mounted on the front ensured the parts would not overhang the front, drop off or cause other incidents.
The robot would then travel to other stations to pick up the remaining three parts, and place them beside or in front of other parts. After traveling around the picking area to get all pieces of differing heights and weights, the robot would deliver the full kit to the end of the line.
The Results
Using their deep industry knowledge and experience, Hyperion guided this automotive parts supplier through a complete system integration. Through these custom solutions, they were able to utilize their existing controls systems while reducing labor costs, better utilizing employee time and improving floor efficiency.
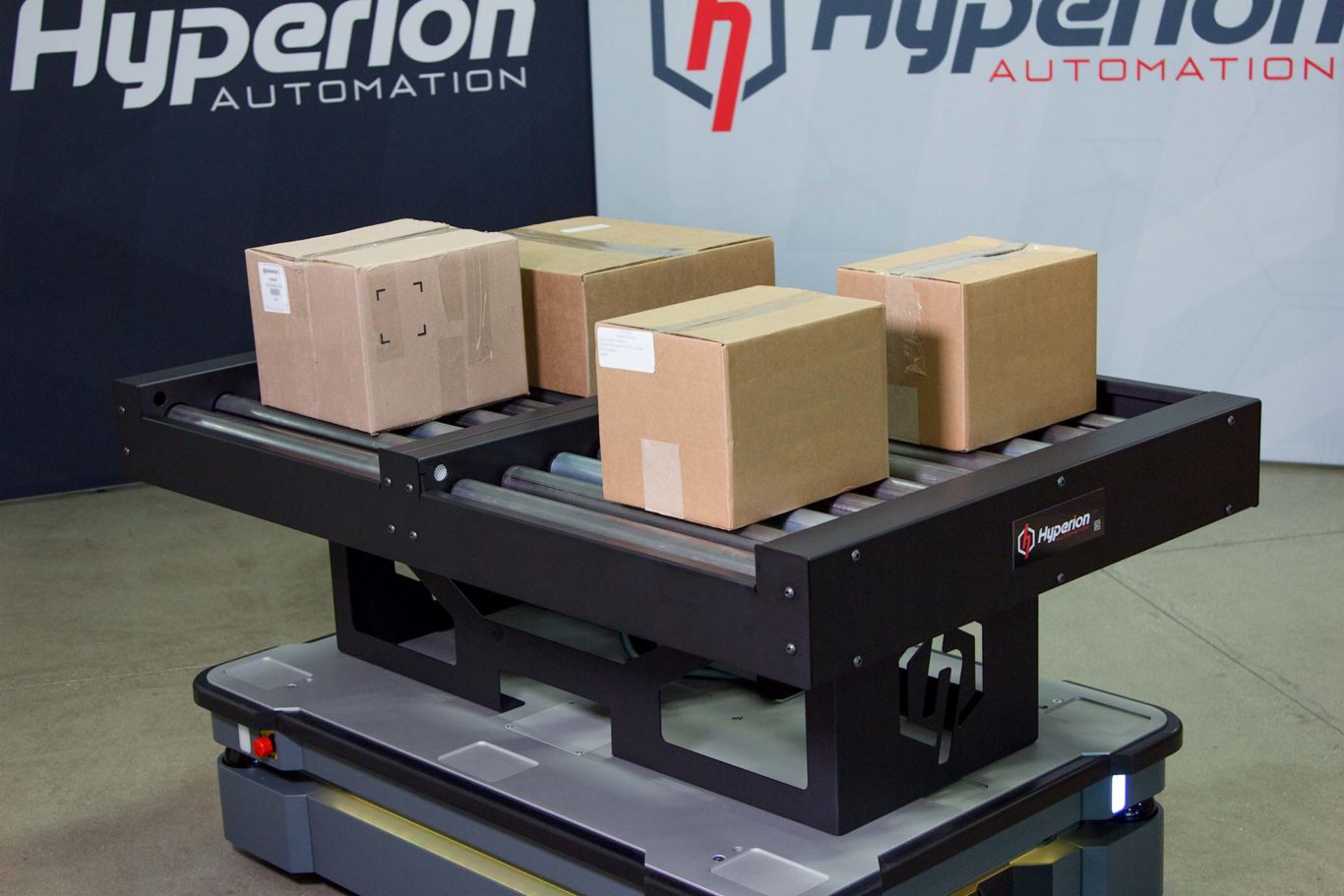
Considering a Top Module for Your AMR Application?
No matter your challenge, Hyperion’s team is ready to rise to it. Learn more about MiRs, AMRs, and the benefits of front- and side-loading top modules on our blog.