As an official system partner, Hyperion Automation recently had the opportunity to join KUKA in a collaborative booth at MODEX 2024 in Atlanta, GA. Together we demonstrated a custom integration of two KUKA autonomous mobile robots (KUKA KMP 1500P AMRs) and a six-axis robot (KUKA Quantec KR210) equipped with AIRSKIN safety technology.
The booth simulated a manufacturing floor, demonstrating how two AMRs synchronously shuttle full pallets of material from a pallet stand to the six-axis robot for depalletizing. Then, using SICK PLB vision systems, the six-axis robot re-palletized the product from one pallet to another.
Simulating Real-World Applications
Both KUKA and Hyperion wanted to create a demonstration that could easily be used in a real manufacturing environment. They looked at how clients integrated their products (e.g., a large airplane manufacturer that uses AMRs to transport planes from A to B or the large warehousing entity that moves pallets of product using several, smaller AMRs). Drawing inspiration from the real world, they began to form an idea for a display.
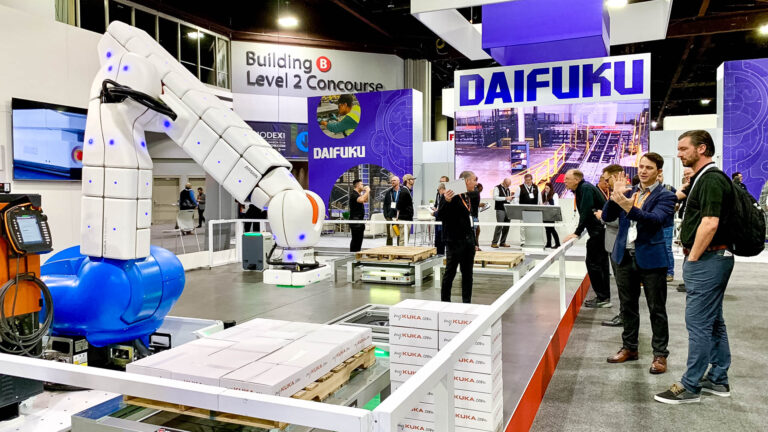
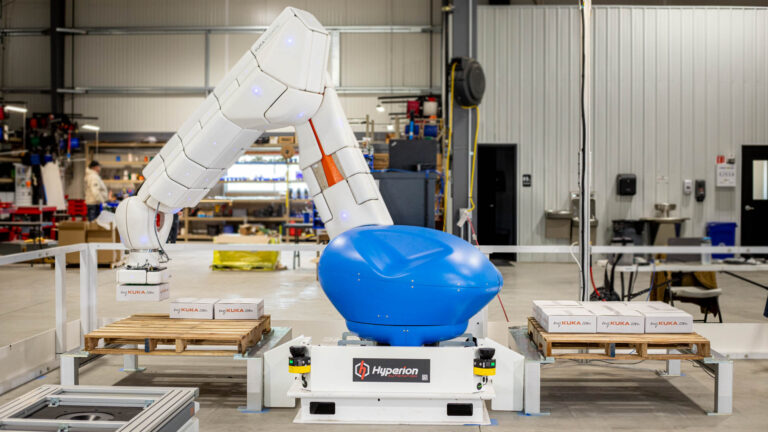
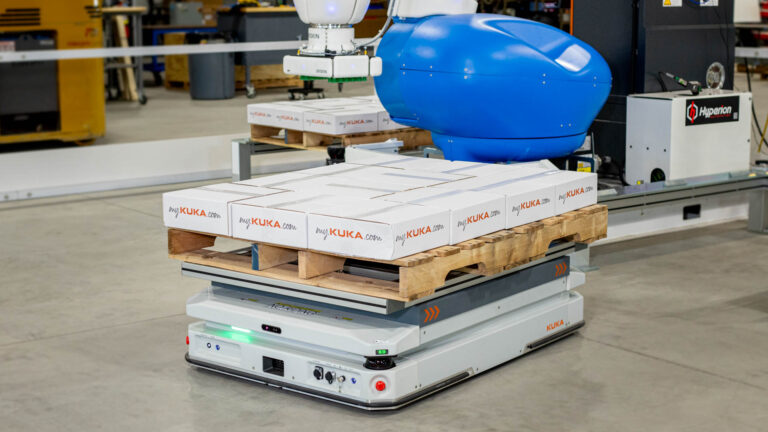
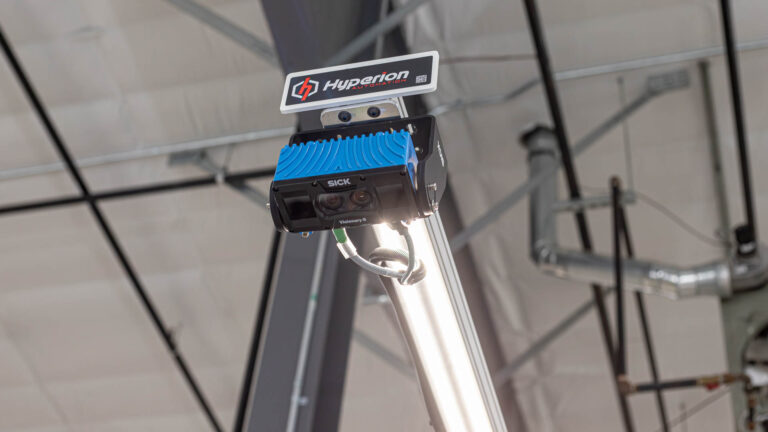
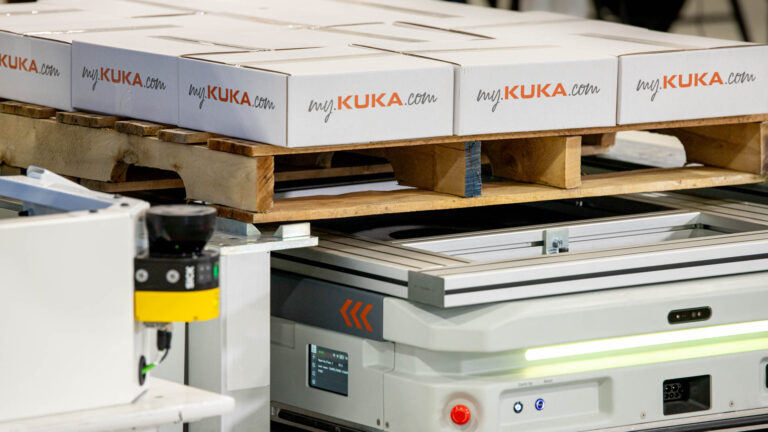
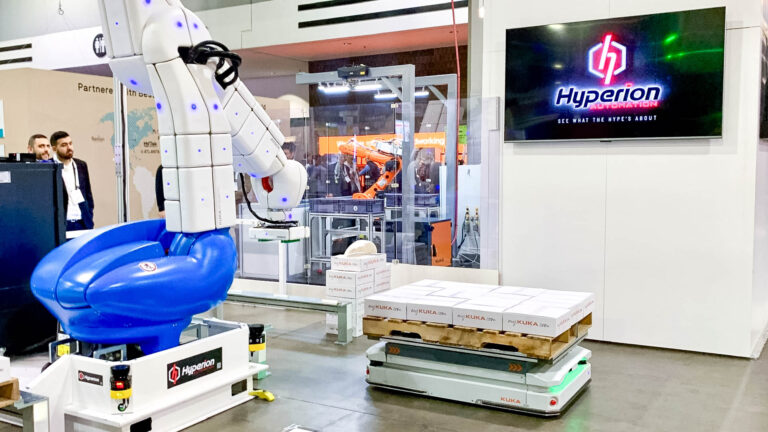
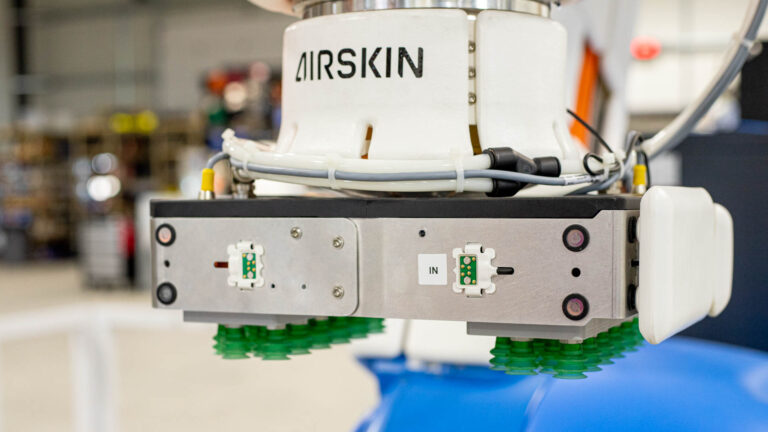
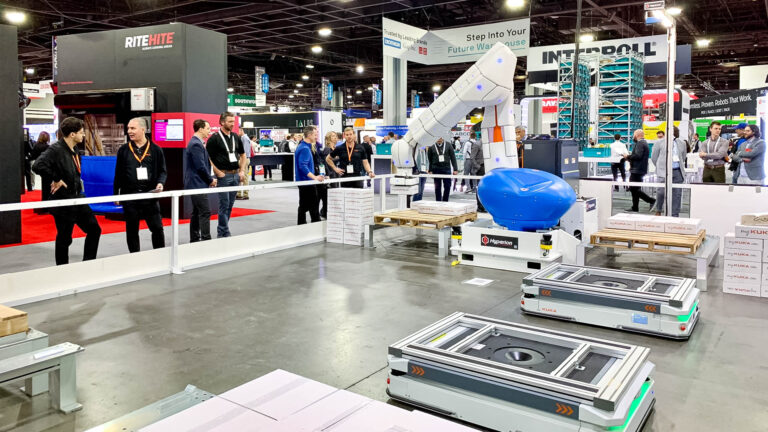
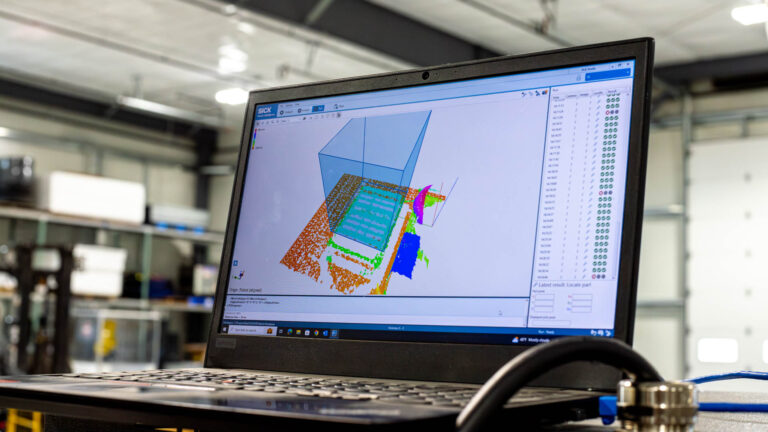
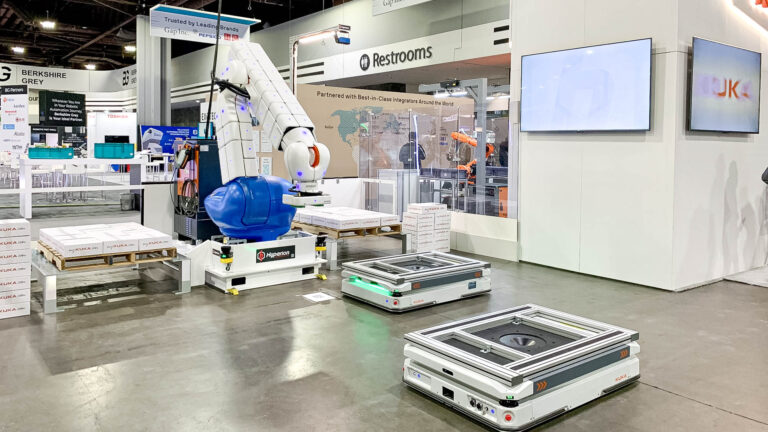
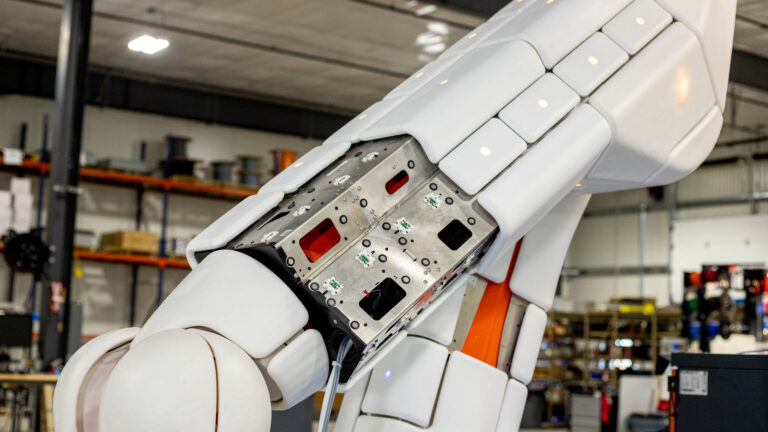
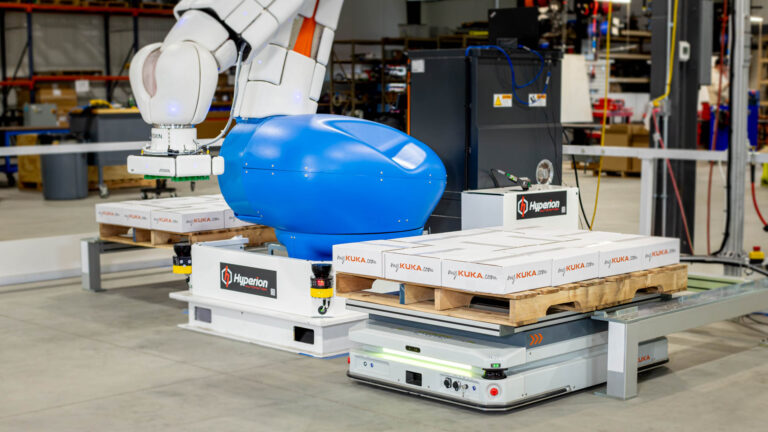
The Project
Vision System
The first challenge for our team was selecting and programming visioning software for the demonstration. We collaborated with SICK to form a lower cost solution for complex visioning needs.
First, the SICK sensors capture an image of the pallet using a 3D camera to determine the boxes’ locations in the robot’s native coordinate system. A single high resolution 2D RGB sensor takes an image and then machine learning algorithms are used to determine the X and Y coordinates of the boxes on the pallet to find the center point of the box within a resolution of ~1mm. The height, or Z coordinate, is found by two 3D infrared sensors using stereoscopic vision in conjunction with a grid of infrared light projected on the surface of the pallet to find the top height of the boxes with a resolution of ~5mm.
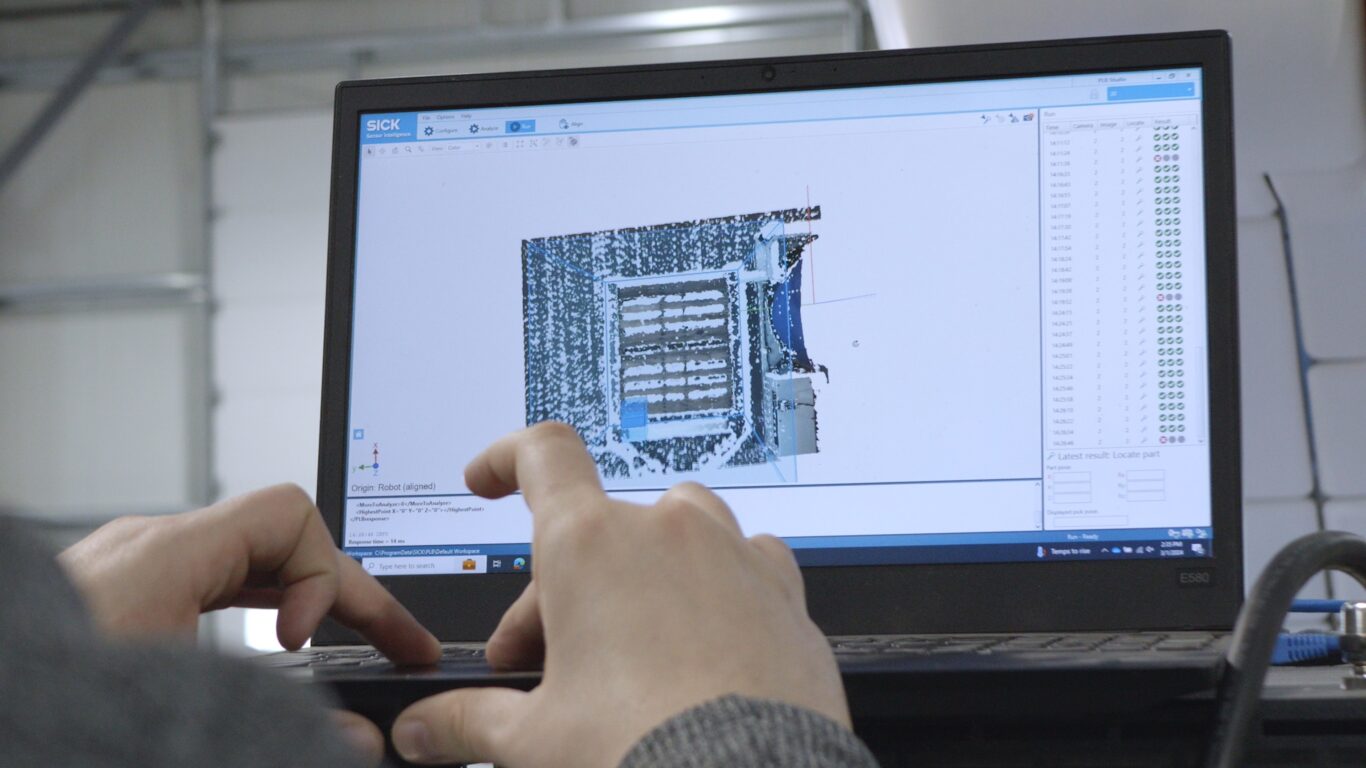
The whole system works together by layering the 2D and 3D images for a complete picture that gives a highly accurate box center point to pick from, with a lower cost than a traditional 3D camera that would be required to obtain X and Y coordinate accuracy within 1mm. This sophisticated visioning technique can run through the entire process in half a second or less. The vision system “talks” to the six-axis robot via high-speed ethernet (using TCP/IP), allowing consistent communication, and use on KUKA robot system without requiring a PLC.
Movement
Meanwhile, both KUKA AMRs move along pre-programmed tracks in the production space, ferrying goods back and forth between pallet stands and the palletizing robot. Their connection to the database allows them to keep track of which pallets are empty or full. This “memory” combined with the programmed tracks indicates where the AMRs should move for each step in the process.
Were these AMRs deployed in a real manufacturing environment, they might also utilize a built-in camera feature to scan QR codes and confirm they’re picking up and dropping off the correct pallet of product. Manufacturers often place these QR codes on the floor to increase the robot position accuracy.
Safe Collaboration with Human Operators
Both the KUKA six-axis robot and the KUKA AMRs are equipped with safety features that make them more desirable in a modern manufacturing space.
Notably, the collaborative six-axis robot was designed to work safely alongside a human operator, enabled by an AIRSKIN safety suit. The AIRSKIN suit panels that coat the robotic arm sense any change in volume and trigger an emergency stop—one small bump to the robot will bring it to an immediate halt.
The AMRs themselves are factory-built with safety sensors. These sensors continuously scan the area around the robot and stop immediately when they sense an obstacle in their path. The safety equipment on all three robots creates a manufacturing experience designed to coincide with human operators in the same workspace.
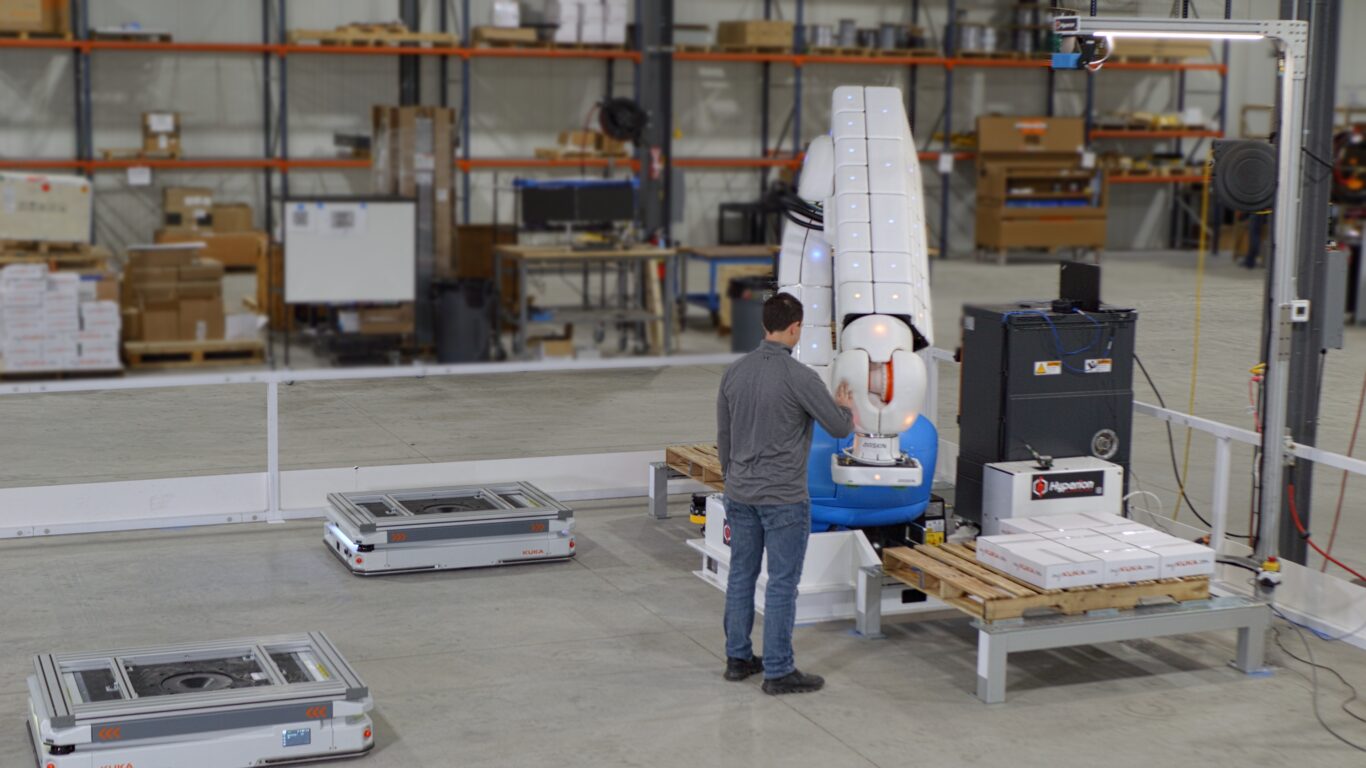
Thank You, Partners & Collaborators
Partnering with KUKA in their booth at MODEX was an excellent opportunity and honor. We are grateful to KUKA for trusting Hyperion Automation, an official system partner, to program and develop a demonstration for their booth at MODEX this year. We’re also thankful for our partners at AIRSKIN and SICK for their significant contributions to the project.
Hyperion + KUKA
Learn more about Hyperion’s partnership with KUKA for automation products and solutions.