At times manufacturing can be a dangerous industry. According to the U.S. Department of Labor Statistics, manufacturers had the second highest rate of workplace illnesses and injuries.
The National Safety Council lists the most common causes of these injuries as:
- Contact with objects and equipment (34%)
- Overexertion and other bodily reactions (32%)
- Falls, slips, and trips (18%)
- Repetitive motion (6%)
- Exposure to harmful substances or environments (5%)
Even as operators interface with automated machines on the factory floor, they’re safer than they would be with an entirely human team—prone to the common mishaps caused by fatigue and exhaustion. The effects of increased automation in manufacturing are already evident in workplace safety trends.
Even over the last decade, we’ve seen significant declines in occupational injury rates (see Chart 1), and we expect this trend to continue as more companies invest in automation technologies that protect their workforce.
An automated factory floor reduces variability creating a more consistent product and a more reliably safe work environment.
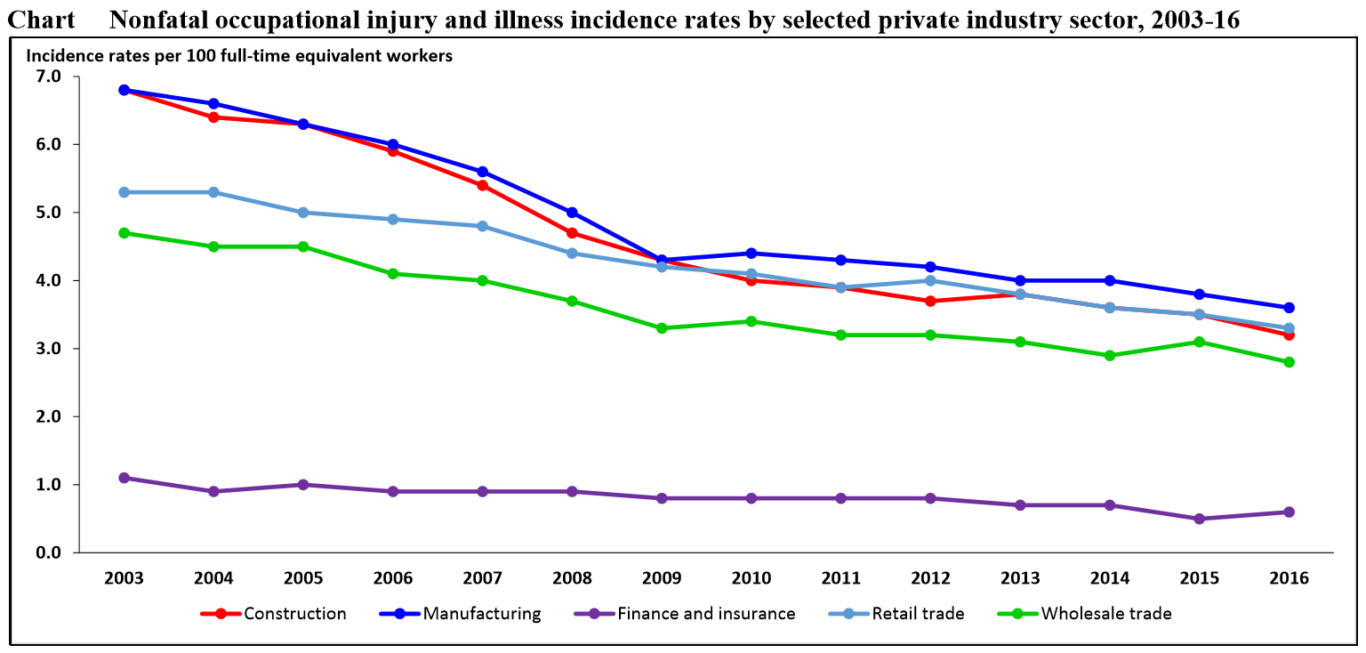
As an automation solutions provider, we’re always looking for ways to reduce injuries from fatigue, repetitive tasks, and heavy lifting. Automation also eliminates exposure to hazardous conditions. With the global labor shortage, it’s more important than ever to keep employees safe on the job.
Spinning Our Wheels
A huge benefit of automation is saving operators from the physical discomfort of manual work. For example, a wheel manufacturer approached us with a serious safety challenge on their floor. Employees were manually unloading 60-pound alloy wheels from a pallet onto an inclined conveyor. Back injuries with this type of repeated motion are common.
Our goal was to eliminate risky heavy lifting. After our team of experts customized an automated solution, the manufacturer increased their throughput from their previous rate of 200 wheels per hour to over 400 wheels per hour. Not only did this solution improve production, but it also protected dozens of operators from potential injury.
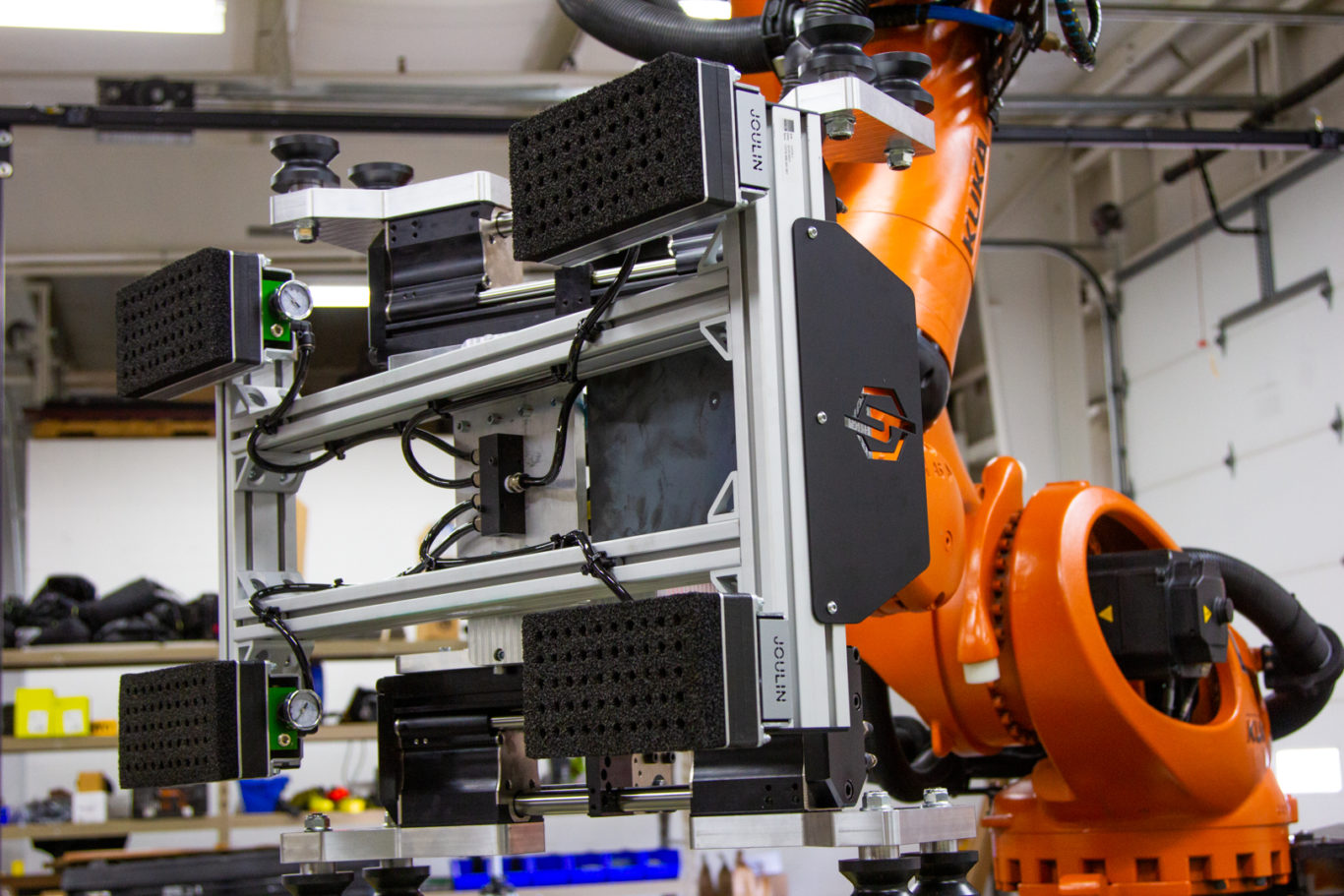
Reducing Repetition
While the wheel manufacturer handled hundreds of heavy wheels, another client was looking for ways to reduce the risk of repetitive movements.
A manufacturer in the furniture industry employed an operator whose primary responsibility was tucking a tiny corner of fabric into cubicle walls, which made it difficult to retain employees in this area. They would need to continually rotate operators to prevent burnout from boredom or injury from repetitive motion.
In response, we designed a machine that could do the work, freeing up the operator to complete more productive tasks.
Avoiding Hazardous Environments
In hazardous environments with extreme temperatures, molten metal, or toxic fumes, robots can become invaluable members of the team.
Robots can fit in tight spaces where operators would normally be trapped breathing in dangerous materials. They can also safely occupy both frigidly cold spaces or the intense heat of giant ovens and molten metal. When manufacturers implement automation, it also keeps their operators from having to touch dangerous chemicals.
We Can Help
In a work environment where constant change is the norm, any effort to create consistency can tremendously improve operator safety. Let us help you keep your workers avoid dull, dirty and dangerous jobs.