When a wheel manufacturer faced a complex problem in palletizing and packaging their products for shipping, they called the experts at Hyperion to solve a multifaceted automation challenge.
Challenge
Having previously worked with Hyperion on another solution, this automated packing cell for the wheel manufacturer provided a completely integrated turnkey solution to a complex problem. With Hyperion’s disciplined process, they paid precise attention to detail while staying responsive to the manufacturer’s evolving needs. Some of these challenges included:
- Labor shortages made it extremely difficult to find and retain talent for a heavy wheel packaging line that ran around the clock.
- The wheels were heavy, requiring strength and care to move them from the end of the processing line to final packaging while maintaining a desired throughput rate.
- Different wheels required different pallets, dividers and sizes of pre-cut polyfoam sheet that demanded precision of the automation system as well as flexibility for conveyors and robots to handle all types of materials.
- The manufacturing floor only had so much space to house automation equipment.
- The cells had to be large enough to allow egress for employees to add new pallets and materials with fork trucks or provide maintenance work on the machines.
Solution
This larger, full system integration required many components to find the just-right solution for the manufacturer’s needs.
Cell Design
The manufacturing cell required numerous interface points. To be successful, the design needed space for:
- Fork trucks to get in and out
- Operators to move rejected wheels and pallets out of the cell
- Operators to move 48” polyfoam rolls into the cell
- Operators to come in and maintain the robots when needed
- Empty pallets and newly finished wheels to load in via conveyors
The design of the cell also maximizes manufacturing floor space while making allowances for operators, fork trucks, materials and machinery (in particular the robots and conveyors) with the ability to handle all possible sizes and dunnages of wheels and pallets without interruption.
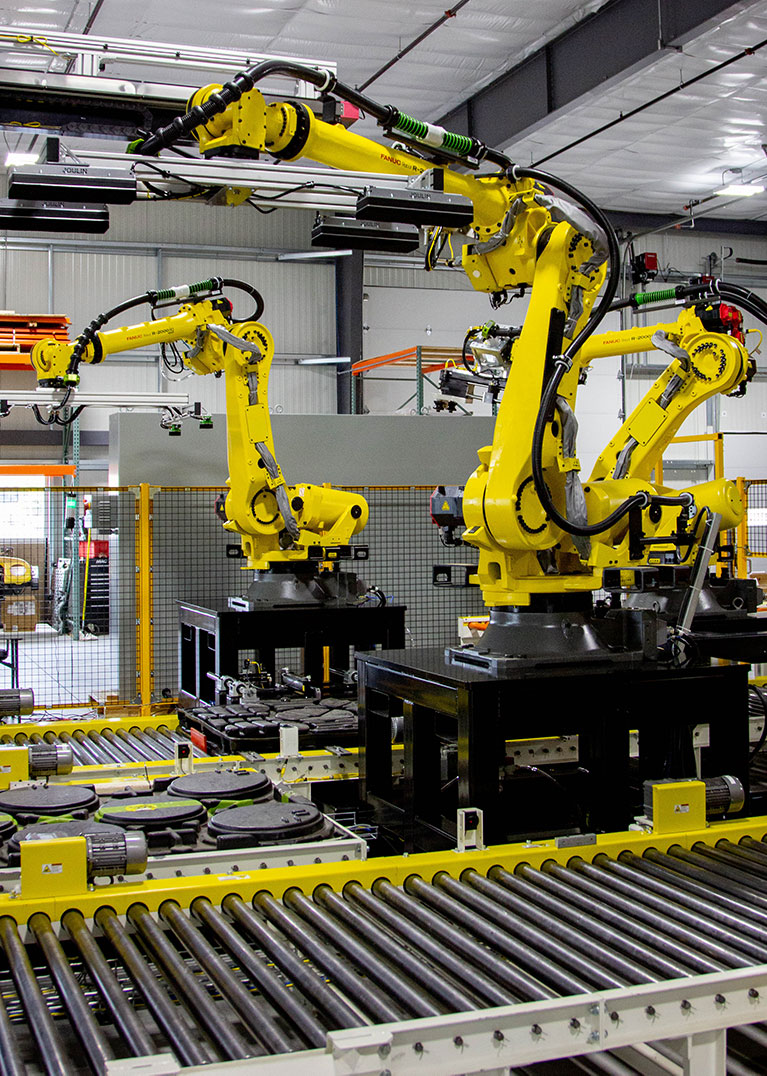
Wheel Robot
To maximize efficiency of the workforce in an already-tight labor market while eliminating the physical strain of lifting wheels, the picking robot gently moves wheels of every size and weight. The robot provides accurate movement from the line to the pallet at a consistent rate.
Conveyors
Conveyors take the newly finished wheels from the production lines to the packaging cell, feeding wheels into a palletizing line. These conveyors were designed to transport all wheels and pallet sizes, types and dunnages. To help align pallets as they index into the palletizing area, the conveyor utilizes pallet stops to align the pallet along the front edge, with a crowder pushing it into alignment on the side.
Vision Systems
As wheels pass through the initial conveyor, a vision system scans the wheels to verify wheel size and type, ensuring consistency and correct packaging materials.
A second vision system guides the robots, identifying divider types as they convey into the cell. The vision system then scans the entire pallet to verify the correct dunnage type for the wheels being loaded while also capturing positional data on X, Y, Z and angular offsets to successfully pick and place each divider, all while preventing incorrect dividers or bases from getting mixed in.
Polyfoam Layer
To save on the cost of pre-cut material and labor, a polyfoam sheeter automatically cuts the material to length on demand—instead of requiring pre-cut sheets and a manual job to place them between rows of wheels. The automated sheeter can also switch sheet size on demand to accommodate anywhere from five to eight wheel pallet sizes.
Automated Bander
In the final step of the process, the pallet is conveyed out of the cell and into an automated bander system. Previously, the banding machine required an operator to line up the pallet and then push a button to band it, but the new fully automated machine now completes the work without the need for an additional operator.
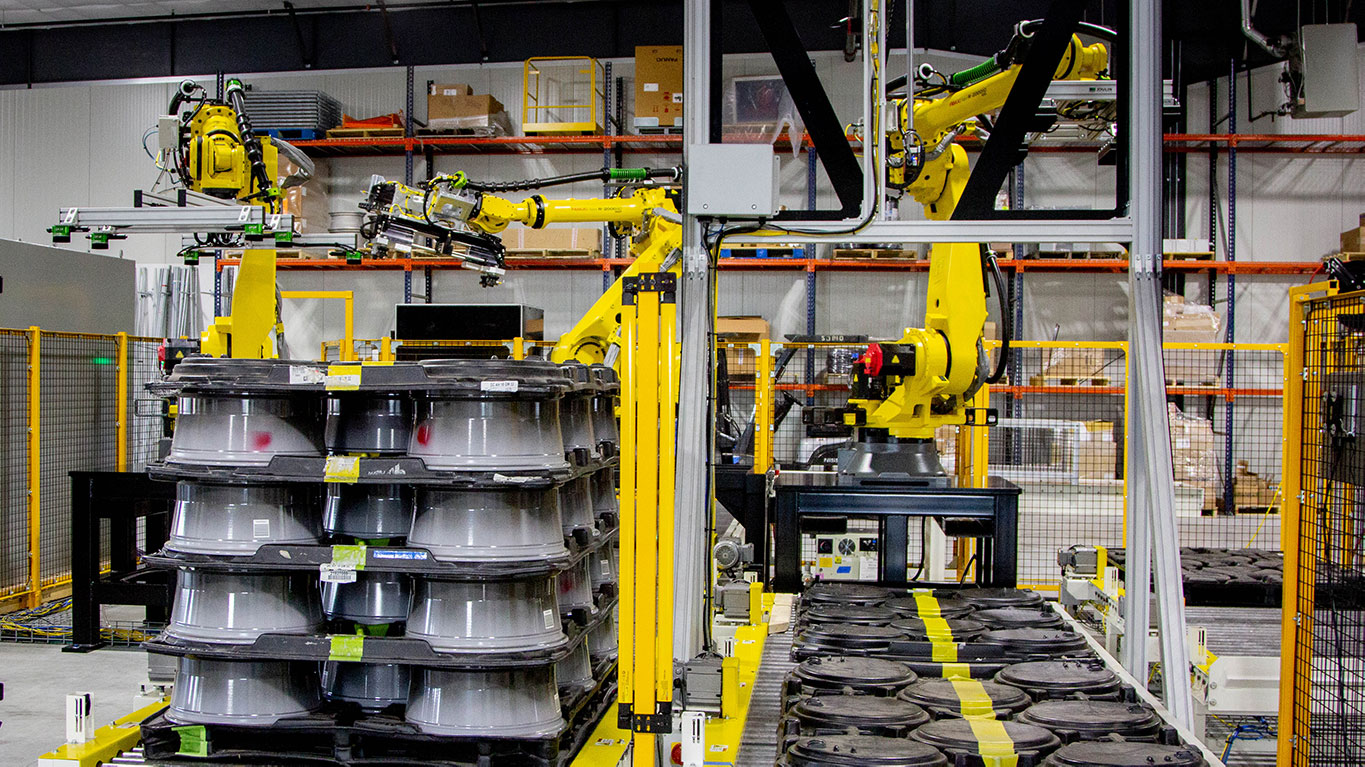
Results
Following Hyperion’s process with a commitment to finding creative solutions, the wheel manufacturer has a fully-automated solution that saves on material costs while reducing the need for heavy manual labor in a difficult hiring environment.
Find a complex solution for your challenge without cutting corners. Talk to our team about your unique automation needs today.