Try to imagine this: a pallet of frozen carrots enters a 330,000 square-foot icy-cold, temperature-controlled building. The bags of carrots are decanted from the pallet into tote bins, which when filled, begin their journey down thousands of feet of conveyor.
Along the way, dynamic routing points use a battery of sensors to direct the totes to one of six large automated storage/retrieval systems (ASRSs), where they are queued in storage racks via automated cranes. When they’re ready for shipment, the ASRS pulls the tote, and it’s routed to one of the facility’s dozens of picking and repackaging stations where they will be placed in cases.
Quick Facts
Client: | Food Processing & Distribution |
Application: | Distribution Center |
Core Solution: | Advanced Integration with Warehouse Management & Controls |
Technologies: | Material Handling, Inspection, Vision, Packaging, Robotics |
Outcomes: | Estimated 60–70% reduction in labor, decreased errors, improved safety and well-being |
Case conveyors then bring cases of frozen carrots to palletizing stations, where they are automatically sorted with scanners and delivered to operators to be placed on the correct mixed-good or “rainbow” pallets with other frozen goods. Finally, finished pallets are routed down pallet conveyors to automated stretch wrapping machines before they arrive at shipping, where they can be dispatched to their final destination.
Now imagine this same process happening for frozen broccoli, frozen dinners, and a dozen other types of frozen foods. Are you still with me? Now imagine all of these processes are happening simultaneously, using the same stations, conveyors, ASRSs, and routing systems. At any given moment, thousands of items are moving through the facility passing through over 100 different routing points.
Conducting this symphony of movements is upper-level software called the warehouse control system (WCS). Through custom integration, systems index and track the pallets, totes, and cases as they move through the warehouse, and they pass this information back to the WCS. Armed with the location and vector of everything, the WCS can issue commands to routing points to send a product to Point A or Point B, and the tracking system reports back the results.
The Challenge
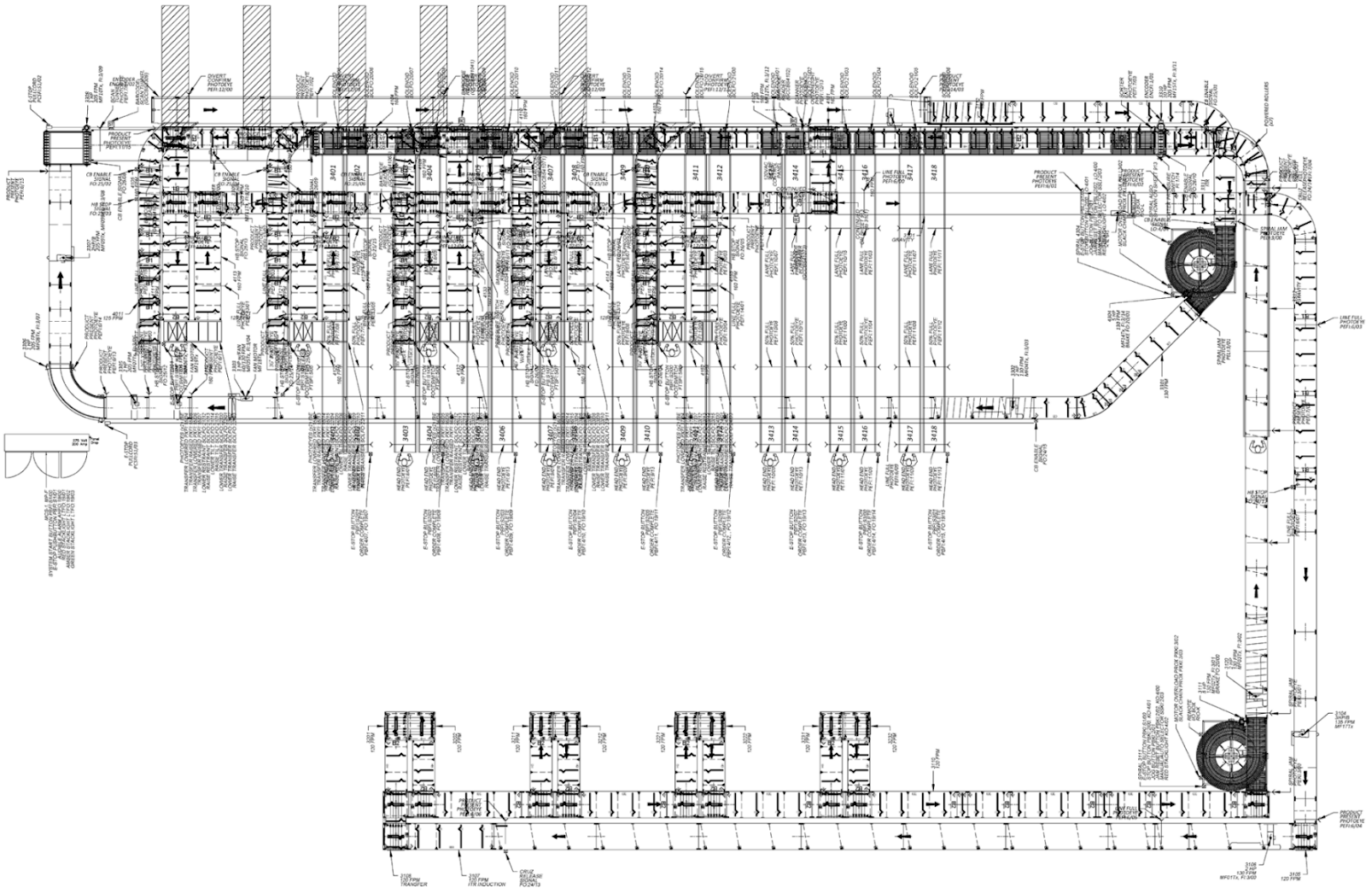
With the construction of their new distribution center, our client was looking to install a highly automated, state-of-the-art warehouse management system. A massive web of conveyor systems would support receiving, decanting, picking, repalletization and shipping processes. Across two independent tote and pallet conveyor systems, the distribution center would also tie together 1000s of feet of conveyors with 6 automated storage retrieval systems (ASRS), dozens of operator interfaces and 122 dynamic routing decision points.
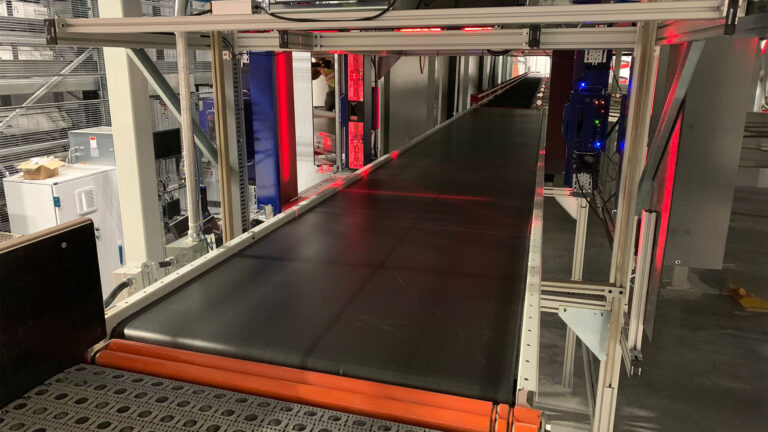
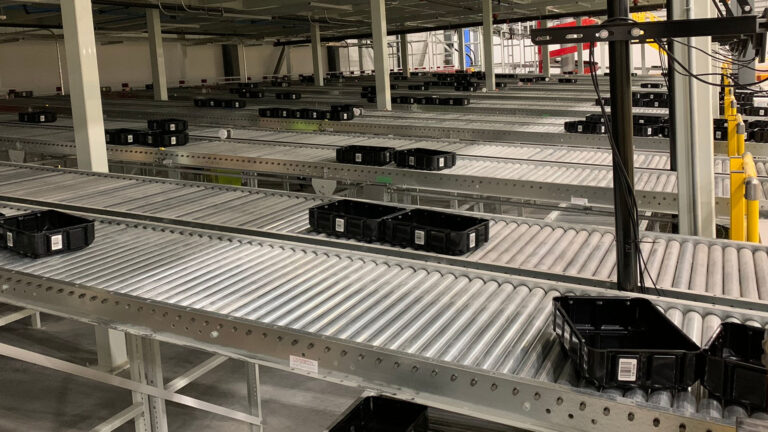
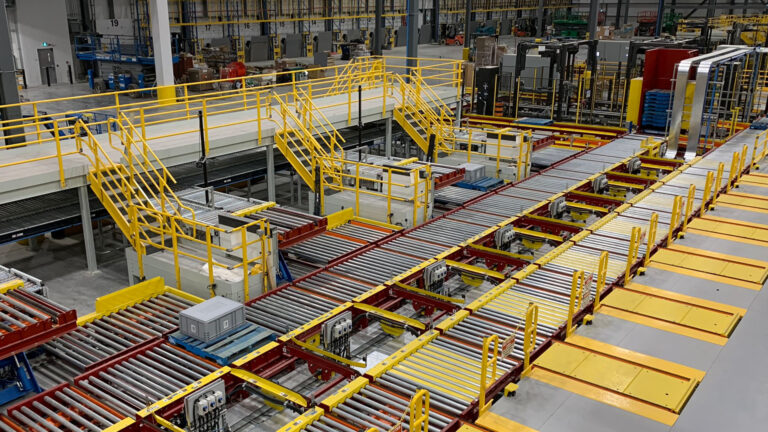
Increasing in Complexity
Historically, warehouse and distribution centers have always entailed large-scale complexities and precise communications. However, the explosion of new technologies to automate and improve distribution systems has seen exponential increases in those complexities.
Overcoming the Language Barrier
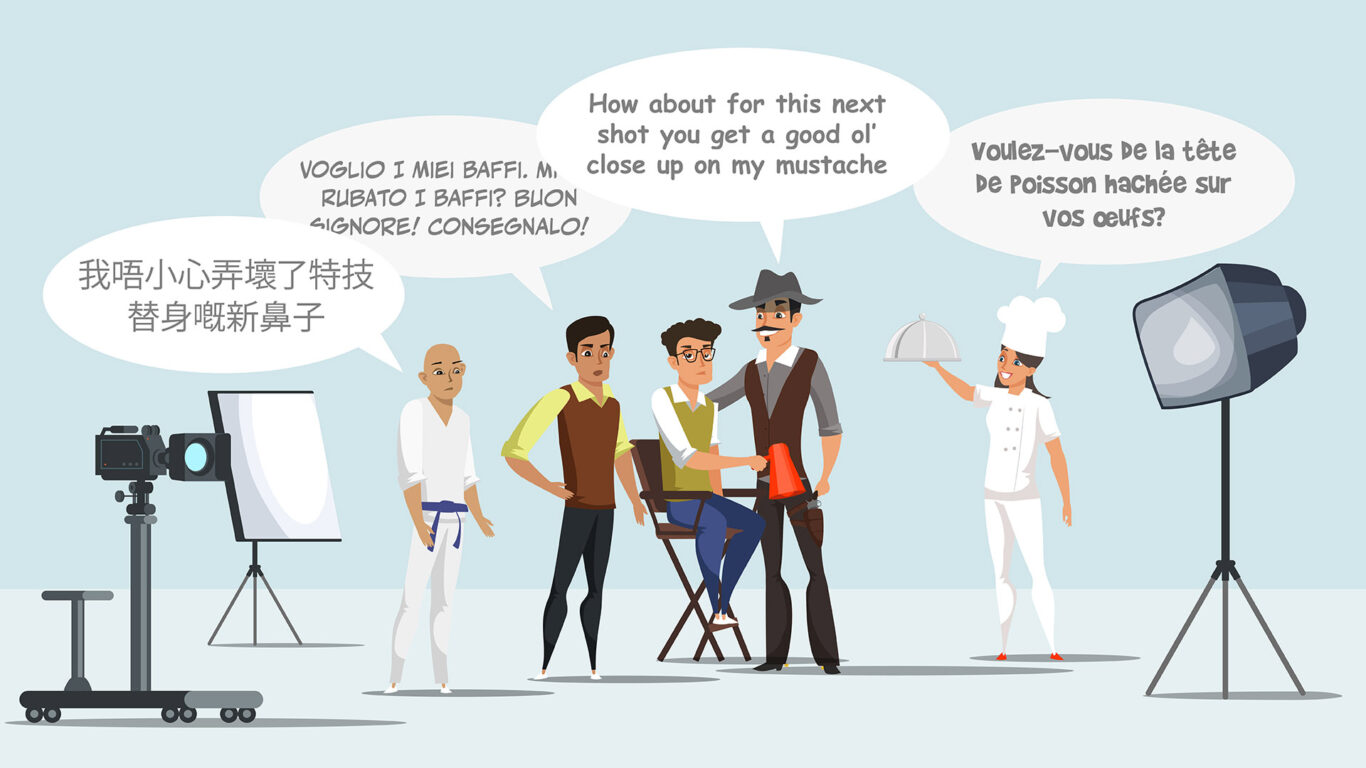
Imagine directing an action movie where you only hire people who are at the very top in their fields.
Your actors might speak English, but your cinematographer might be Italian, craft services would be provided by a Michelin-star chef from Southeast France, and your Hong Kongese martial arts coach might only speak Cantonese. You would also need to hire the best translators you could find to make sure everyone would be able to communicate with each other.
Procuring the top automation solutions for your distribution center is not so different. Manufacturers are invested in honing their engineering to make the best possible camera, robot or self-driving vehicle—they’re not as invested in making it integrate with other manufacturers’ (who are often their competitors) products. You might assume that at least some of these products are plug-and-play, but this is rarely the norm.
In the case of our client, we had 100s of devices and systems (sensors, robots, ASRSs, controllers, etc.) from a dozen different manufacturers, each of which had their own sub-systems, controls, and unique languages/protocols for communication.
The key challenge in an integration project of this magnitude is to get over 1000 separate devices and systems to communicate with the Warehouse Control System (WCS) and one another in real time.
The Solution
Universal Translators
Our client engaged Hyperion Automation because over the years, we’ve learned how to speak fluently and translate any protocol. Our expertise allowed the client to avoid lengthy pauses in the build process because we don’t need to contact the maker’s tech support team for every tricky decision.
As a result, Hyperion was able to provide both the required technology and the technical know-how to get everything speaking the same language.
Anticipating Latency for Just-in-Time Data
Even a few seconds of hesitation at routing points can cascade to costly shipping delays, especially when they’re performed hundreds or even thousands of times per hour. In order to make real-time decisions without a massive bloated database, you need just-in-time data.
Our technical experts anticipated this need, and provided solutions to get the right information to the WCS before it needed to make a decision. For example, we know that there is inherent latency in any communications system—requesting routing information from a WCS is no different. However, oftentimes to calculate the right routing data, the WCS will need to query higher-level software or offsite servers, adding even more latency. We take the time to understand the structure of the communications and determine the latency so we can design our systems to accommodate. Factoring in travel speeds, we strategically positioned barcode cameras and sensors ahead of decision points so we could request routing instructions earlier and avoid delays at the fork.
The Tech
To get the automated conveyor system integrated with other systems, machines and the WCS, we installed and configured:
- 600+ sensors, including photo-eyes, ultrasonic sensors and proximity switches;
- Dozens of barcode scanners and multi-sided barcode scan tunnels;
- 6 main 5-door control panels and programmable logic controllers (PLCs);
- 7 remote I/O enclosures;
- And 100s of variable-frequency drives (VFDs) and intelligent MDR control modules.
The Results
60–70% Reduction in Labor
We predict that the automated distribution center system will result in a 60–70% reduction in manual labor, which frees up workers for more important tasks.
Scalability
Because Hyperion Automation planned the communications integration from the ground up, the system is well-positioned to scale—our client will save significant cost and time when it comes time to add new lines or technologies, such as autonomous mobile robots (AMRs), robotic pickers, or palletizing/decanting cells.
Improved Employee Safety and Well-Being
Forklift accidents are responsible for an average of 88 human fatalities and over 7000 injuries in the United States each year, making them one of the greatest threats to job safety in warehouses and distribution centers. Combined with ASRSs, smart conveyor routing systems for our client have significantly reduced the need for forklifts, substantially increasing workplace safety.
Automations have also replaced much of the dull or repetitive manual processes, which has freed up workers to engage with more interesting and fulfilling work. Meaningful work and engagement are connected to numerous positive outcomes, including improved productivity, better physical health and better mental-health for employees.
Fewer Errors
Advanced product tracking and automated barcode scanners provide a significant reduction in errors when compared to systems that require manual data entry or reads. Unlike humans, machines don’t get distracted or zone out during the work day. And in the unlikely event that errors do occur, data and logs exist to easily track down those errors with little guesswork.
Let’s Get Started
If you have a complex integration project, or if you would just like to talk more about integration technology with a specialist at Hyperion Automation, send us message!